Chatter is a troublesome issue in machining, but knowing its mechanics can help to tackle the causes and reduce it. Tool selection, workpiece instability, and cutting conditions all will cause chatter.
So, learning how to manage machining chatter enables us to handle it proactively. With tailor-made solutions and real-world examples, manufacturers can improve their machining processes and get better results.
Table of Contents
ToggleWhat is Chatter in Machining?
The chattering definition refers to “vibrations and noise, which leads to poor surface finish, reduced tool life, and increased machine wear.” Machinists usually refer to chatter as “sensitive cutting” or “resonance.” when it occurs, the machines produce a high-pitched wailing sound, and the chip strips generated from the tool are thick and unstable.
The dynamic interaction between the cutting tool and workpiece creates varying forces, causing vibrations. Uneven material removal, improper spindle speed or feed rate selection, inadequate tool stiffness, and chatter-prone workpiece materials are the main sources of these vibrations.
Note: Regularly check machines and tools to catch issues that could lead to machining chatter. That way, you can avoid damage and keep your machining running smoothly.
Understanding the Mechanism of Chatter
During CNC machining, you can experience two types of machining chatter. Some of them are as follows:
Tool Chatter
Vibration is a common problem when utilizing CNC milling cutters for cutting. Once they have started trimming, they add distinct features as the vibration is transmitted to the workpiece. As a result, friction between the tool and the workpiece increases, and the chatter becomes louder.
Workpiece Chatter
Offsets and vibrations can occasionally occur if the workpiece is placed incorrectly on the milling machine’s work table. So, as the thin wall of the part moves towards the cutting tool, it might start to shake.
You should keep in mind that some chatter is difficult to avoid. If the vibration during milling is greater than 100µm, the surface of the workpiece may get scratched. If quality is important to you, you should look into how to reduce tool chatter.
What Causes and Consequences for Chatter in Machining?
The chatter in machining can be a real buzzkill – it can cause uneven cuts, poor surface finish, and even damage to the machine. To prevent this unwanted vibration, it’s important to understand its causes and consequences.
Tool Geometry
Incorrect tool geometry can create vibrations, leading to chatter. For instance, When the slope angle and negative rake increase, the tool wear decrease, which increases the surface roughness.
Machine Setup
Poor setup of the machine, like incorrect parameters or wrong workpiece holding, can cause vibrations resulting in machine chatter. For example, when you place your CNC machine on a soft or carpeted surface it also increases the vibration.
Cutting Conditions
Excessive forces, high speeds, and improper feeds can also contribute to chatter. If these occur it makes the workpiece surface rougher than desired. It also causes burn marks or scratches.
Lack of Rigidity
Another factor is the lack of rigidity in the machine or workpiece setup. If it’s too flexible, it can lead to excessive movement and instability. Rigid design and stable mounting can help.
In addition to these main causes, other details can also affect chatter. Things like material properties, and cutter runout can have an impact as well.
Useful Ways to Reduce Chatter in Machining
In this section, we’ll provide in-depth knowledge of “how to reduce chatter”.
To reduce chatter in machining, some techniques can be applied. These techniques try to minimize the vibrations during the machining process, for smoother and more precise operations.
Using an Appropriate Work-Holding Method
Choosing the right work-holding solution and maintaining CNC machining tolerances are crucial in preventing problems like chattering. To maintain component surface quality at low RPMs, use a tool holder with end face and tape contact to provide optimum stiffness during milling. Workholding equipment, such as vices, vacuum tables, or chucks, must exert sufficient force to secure the workpiece in place.
Avoid clamping only one end of a long, thin workpiece when utilizing jigs and fixtures. Generally, thin-walled components have trouble absorbing shocks, which leads to chattering. Filler materials can increase rigidity and decrease chattering, therefore, it is advised to use a tailstock or sturdy rest frame when creating such components. If proper work-holding methods are prioritized, machining outcomes can be enhanced.
Tool Selection
When it comes to reducing or eliminating chatter, the tool selection can make a big difference. It is true that some cutting tools produce more vibration than others. So, it is important to consider some factors while choosing tools:
- Consider coating of cutting tools: When it comes to performance and vibration production, a cutting tool’s coating can make a big difference. Tools with the right coatings last longer, vibrate less, and produce less vibration when machined. For example, DLC coatings.
- Evaluate the aspect ratio of the tool: Chatter is more likely to occur with tools that are long or thin because they are more susceptible to deflection and vibrations. Choose shorter tools with a wider diameter if you need to make precise cuts. This strengthens the tool and decreases the possibility of chatter.
- Pay attention to correct geometry: The stability and vibration properties of a tool can be affected by its substrate geometry, such as its flute design for CNC machining and edge arrangement. Vibrations or chatter can be reduced by using a cutting tool with the right substrate geometry.
- Keep blades sharp: Make sure the blades are sharp and in good condition; this will lower the amount of force needed while cutting with CNC milling machines. Maintaining the cutting tool by sharpening or replacing dull blades is critical for peak performance and minimal chatter.
Develop an Optimal Machine Strategy
In traditional milling, the amount to which the cutter contacts the workpiece varies. Vibrations can be reduced by keeping the milling cutter under a constant load as it travels along the tool path. Instead of increasing the depth of the cut, you might try modifying the toolpath to keep the engagement constant.
Moreover, you also have to think about the spindle configuration. For instance, if resonant chatter is the cause of vibrations in the machining process, switching to a different spindle design may help. Small changes to the RPM of the machine, such as raising or decreasing it by about 5%, can help reduce resonance vibrations.
Some CAM software has tools that let you change the spindle speed in a consistent way. This gives you more options for dealing with chatter-related problems. For example, you can use a vertical machining process in which a vertical machining center (VMC) involve. In this, the spindle is placed vertically to the tool holder and cut the top of the workpiece.
Setup and Maintenance of Machines
It is important to set up your CNC machine on a flat, smooth, and uniform concrete floor. Machine chatter can occur more or less frequently depending on how the machine’s parts are arranged and placed. Don’t put the machine on soft or bouncy surfaces that can make the movements worse.
Think about using anchors to keep the machine from moving around on the floor. This helps keep things from moving or shaking too much, which can cause them to chatter. Also, fix the machine’s feet to ensure they are firm and level. This will further reduce the chance of chatter while machining.
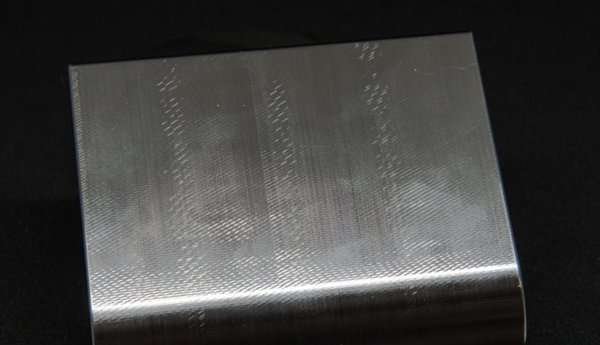
Get Machining Services at XinCheng
Various small problems can occur during machining operations, such as chatter, which can have a negative effect on the final product. When that happens, you need a CNC machining expert to assist you.
As a professional CNC machine shop, XinCheng is committed to providing exceptional CNC machining services. Our advanced technology and experienced team enable us to handle projects of any complexity with precision and attention to detail.
We can provide high-quality components that have been made according to your requirements, whether you need milling, turning, or multi-axis machining.
Read more: Cost of CNC Machining
Conclusion
There is nothing worse than chatter in machining – it can cause uneven cuts, poor surface finishes, and even machine damage. It is crucial to understand the causes of this unwanted vibration in order to prevent it. Various causes contribute to chatter ranging from machine setup to machine maintenance.
FAQs
How does chatter affect machining results?
The chatter in machining can lead to poor surface finish, dimensional inaccuracies, and shortened tool life. It can also increase the wear and tear on the machine tool, resulting in reduced productivity and increased maintenance costs.
Are there any advanced techniques to control chatter in machining?
Yes, advanced techniques such as active chatter control systems exist to monitor and control chatter during machining processes actively. These systems use sensors and actuators to detect and counteract chatter in real-time, resulting in improved machining stability and productivity.
What role does machine rigidity play in chatter?
Machine rigidity refers to the stiffness and stability of the machining setup. Insufficient rigidity can amplify chatter by allowing excessive tool or workpiece movement.