Fillets and chamfers are two different features in design engineering. Product designers use them to reduce eliminated sharp edges and give products a fine and complete surface. These design engineering features benefit the part production, assembly, and utilization.
Incorporating these features in your parts helps to reduce stress concentration and enhance the physical properties of your products. Therefore, it is essential to get a comprehensive fillet vs. chamfer comparison and understand their differences to choose the ideal one for your project.
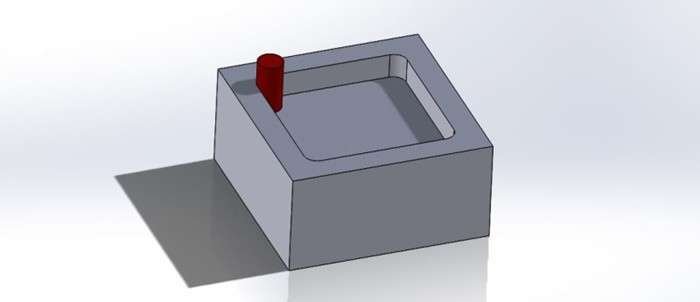
What is a Fillet?
A fillet is a rounded feature on a workpiece’s internal or external corner. This design enhances the mechanical characteristics of load-bearing parts.
The standard type of fillet mechanics includes convex, miter, and concave fillets. However, fillets are generally concave on the interior and convex on the exterior.
These fillets are vital in the manufacturing of mechanical parts. Machinists often use them in soldered, brazed, and welded joints. Besides, you can easily machine fillets in a workpiece with a milling cutter.
Purpose of a Fillet
A fillet is the ideal design feature for eliminating sharp edges and ensuring a low-stress concentration in part. The fillet edge enhances a component’s load-bearing capacity and strength. They allow better material flow in metal-casting and plastic injection molding processes.
Besides, filleting helps reduce stress in a product by distributing high-stress concentration over a larger surface area. This improves the aesthetics of a product and prevents the stressed component from deformation rapidly.
What is a Chamfer?
A chamfer is the beveled or sloped interior or external corner on a part. It gives the uneven edges of your part a more uniform appearance, preventing the edges from deteriorating.
The standard angle for a chamfer typically ranges from 45 – 60º from the horizontal. However, a chamfer at a 45º angle to the horizontal is suitable for removing burrs from drilling operations. Chamfered edges allow features like bolt or screw heads to stay below the surface when you use undercut in machining.
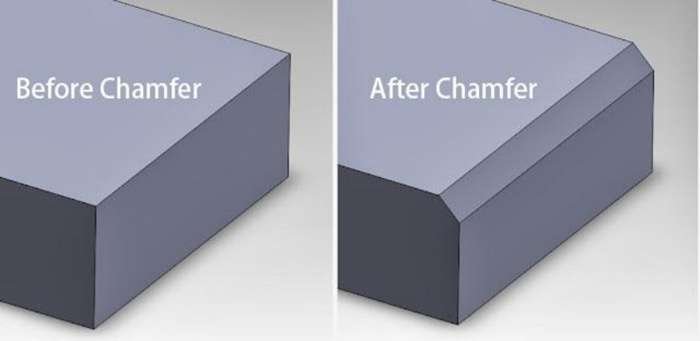
Purpose of a Chamfer
From the chamfer definition above, you will note that it primarily enhances the aesthetics of your parts by easing any sharp edges. Chamfers are suitable for deburring because it eliminates rough ridges and edges in machined parts.
In addition, chamfers are forgiving so they support the easy assembly of components. Moreover, the male and female components slide against each other in an assembly without worrying about the part’s functionality or increase in production costs.
When to Use a Fillet or Chamfer?
When to use a fillet or chamfer in parts is a major dilemma machinists encounter when drafting a design for machining. Adding the wrong feature to your parts may increase production costs and reduce efficiency.
Therefore, it is crucial to understand the fillet and chamfer phenomena to determine when to use a fillet or chamfer for your product.
Edges of a Part
It is advisable to round off all corners of your product’s design to prevent risks of accidents during inspection and handling. However, the chamfer’s sharp edges make it unsuitable for your product’s edges as it is likely to cause hazards while using. Therefore, you may want to use a fillet in such a situation.
Aesthetic
Fillet engineering blends the intersecting point of two surfaces to create an appealing and ergonomic design. Add fillets across the edges of your product if it requires an aesthetically appealing exterior design. However, it would be best to consider the radius size to avoid errors. The fillet design improves with a higher radius because a high-radius fillet relieves stress better.
On the Hole
Using a fillet corner for your part is not advisable if there is a hole where bolts or screws will be driven in your design. It prevents seamless movement of the screw or bolts into the hole; hence, you must use a chamfer. The sharp edges of the chamfer allow smoother pin movement through the hole and make fastening easier.
Fillet vs. Chamfer: What are the Differences Between Fillet and Chamfer?
A fillet corner eliminates sharp edges in a product by adding curved radii to its corners. Machinists often use them on corners where two surfaces intersect at a sharp or acute angle. Therefore, fillet engineering enhances the aesthetics and safety of a product, improving its strength and durability.
On the other hand, chamfer adds a sloping edge that removes sharp edges or corners on manufactured products. They are best used on parts with surfaces connecting at an edge. Aside from improving a part’s appearance and safety, chamfer aids easy assembly of manufactured components.
Although both designs help ease sharp edges and reduce stress concentration, chamfered edges exhibit poor stress resistance since they cannot disperse stress over a broader surface. Even though the significant difference in these designs lies in their shape, below is a brief chart showing the difference between fillets and chamfer.
Fillet | Chamfer | |
---|---|---|
Safety | Fillets make parts safer to handle due to the absence of sharp edges. | Sharp edges on the chamfers cause injury. |
Machining Time | Machining curved edges require patience because they are complex. As a result, fillet engineering takes longer than chamfer. | Chamfer machining is faster filleting. |
Machining Cost | The cost of machining fillets is relatively higher than chamfer. | Chamfers are cheaper than fillets. |
Coating | Machinists often use fillets when a product requires coating. | The sharp edges of the chamfer make it incompatible with coating, as it can easily peel off. |
Cutting Tools | Machinists use special cutting tools in machining fillets of varying radii. Therefore, the radius of choice determines the right cutting tool for use. | Chamfer machining doesnt require multiple tools. Hence, you can use one cutting tool to produce different chamfer sizes. |
Stress Concentration | Fillet spreads the stress over a larger radius, preventing the part from deformation. It is ideal for the external part. | Chamfered edges can expose the material to deformation because it concentrates stress on the part. |
Considerations for Choosing Between Fillet and Chamfer
Several factors come into play when choosing between a fillet or chamfer. Below are factors that will help you decide if your product requires a fillet or chamfer.
Part Assembly
Avoiding any interference in chamfered edges is crucial because they usually function as a lead-in in simple part assembly. As a result, the exterior chamfer must be larger than the interior fillet and interior chamfer when assembling the exterior chamfer with the interior fillet and chamfer.
Additionally, it is essential to ensure that the exterior fillet is larger than the interior fillet and interior chamfer when assembling the exterior fillet with the inner filler and interior chamfer.
Stress Concentration
The transition area of the fillet is even and without any edges or sharp points, in contrast to the slope in a chamfered corner. However, both ends of the bevel will create crisp, sharp corners with the part outline regardless of how the slope angle shifts. These corners are usually dull and not sharp. Hence, fillets are the perfect mechanism for reducing high-stress concentration in your parts.
Manufacturing Process
Adding a fillet parallel to the machining axis is more straightforward than adding a perpendicular fillet. It costs more to add a fillet perpendicular to the machining axis. However, the price of such parts will increase significantly. Hence, using a chamfer perpendicular to the machining axis is the ideal choice.
You can use a single tool to create chamfers in multiple sizes. However, it would help if you used a tool with a specific radius to create a multiple-sized radius. Moreover, a chamfer may require less machining duration in a manual operation than fillet machining.
Specific Application
The intended end-use of a product often determines the choice between a fillet and a chamfer. For example, functionality and longevity may be the primary requirement for mechanical or industrial parts. Similarly, aesthetic appeal may be a priority for consumer products.
Cost
Chamfer is the best option for external surfaces and the product’s plane when no special design requirements exist. Conversely, use fillets for the side wall of a part’s inner cavity as the cutter tool follows a side-edge cutting technique leaning the radius as it turns at corners.
However, a chamfer offers more cost-efficient machining than a fillet. Therefore, chamfers are the ideal choice if you need a low budget for your design.
Products Aesthetics
Most product engineers enhance the aesthetics of their products with fillet and chamfer. However, it would be best to choose between fillet vs. chamfer depending on the aesthetic requirements of your products. Besides, fillets are commonly used in industrial design because they enhance the final product’s aesthetics than chamfers.
How to Make Fillets and Chamfers Less Costly?
Even though chamfer and fillet engineering can improve your product’s aesthetic appeal, they will increase the machining time and cost. However, below are helpful tips on how to reduce costs for making your fillets and chamfers.
Use Standard Tolerances if Possible
It is advisable to employ standard tolerances in machining your fillet or chamfer. This is because machining with tighter tolerances requires consistent inspection of chamfers which will increase the cost of your product.
Low or High Volume Production
A product costs more per unit if manufactured in one prototype. As a result, adding a fillet or chamfer design is not a cost-effective choice. However, the cost per unit barely increases for low or high volume production. Therefore, adding fillets to chamfers in large-scale production is relatively cost-effective.
Material Selection
Use materials that cost less and are easier to machine to save production costs. Some materials are difficult to machine, requiring special tools and extended machining times. This factor leads to an increase in the production costs of fillets and chamfers. Therefore, use alternative materials such as engineered composites and plastics which you can mold with built-in fillets. It helps to avoid the need for post-processing operations.
Design Optimization
Examine the design requirement of your product to determine if all the fillets and chamfers are crucial. Consequentially, you can remove unnecessary features and save material.
More importantly, use fillet and chamfer sizes according to functional requirements while reducing material. Additionally, you can achieve similar results at reduced cost with smaller radii or chamfer angles.
XinCheng Helps to Create Necessary Fillet and Chamfer
XinCheng is the ideal and reliable partner for you whenever you need the help of professionals choosing between fillet and chamfer for your parts. With extensive CNC machining capabilities, our team of experienced engineers possesses the right skillsets to handle all your prototyping and manufacturing needs. Contact us today to start a new project!
Read More: CNC Machining vs 3D Printing
Conclusion
This fillet vs. chamfer comparison has given you a detailed look at two common edge design techniques. Products with fillets last longer and can withstand greater stress or load, while chamfers are best used when designing components for an assembly.
However, it is crucial to understand the differences between fillets and chamfers because it influences a product’s safety, machining cost, longevity, cost-effectiveness, aesthetics, and practical design.
FAQ
What tool do I need to make a chamfer?
You can make chamfers using standard tools like a chamfer cutter or chamfer mill. A chamfer mill removes the sharp edges left behind during machining operations.
Which is stronger: a fillet and a chamfer?
A fillet enables improved stress flow than a chamfer. The fillet has a stronger edge design which aids its load-bearing capability and superior fatigue resistance of a manufactured part. Therefore, the fillet is much stronger than a chamfer.
What are the common uses of fillets?
Machinists typically use fillets in machining architectural parts like pulleys, railings, and brackets. These fillets help ease the sharp edges of manufactured parts and make handling safer.