Manufacturers often have to fit several parts to make a whole during fabrication. Sheet metal welding is a crucial manufacturing process that helps join and assemble metal structures. However, it’s a relatively complex process that requires technical skill to ensure your fabrication meets industrial standards.
This article introduces you to welding sheet metal, including various techniques and surface orientation, and provides expert tips for making high-quality welds.
Table of Contents
ToggleWhat is Sheet Metal Welding?
Sheet metal welding is a process that involves welding thin metal sheets together under high temperatures. The welding process involves heating the workpieces to their melting point or beyond till they fuse together, forming a solid continuous bond.
Sheet metal welders work in various world industries, including aerospace, automotive, marine, electronics, assembly plants, etc. Like other manufacturing processes, making high-quality welds requires skill and expertise.
Different Techniques of Welding Sheet Metal
Are you concerned with how to weld sheet metal? There are several welding techniques, each having one advantage over the other.
MIG Welding
Metal inert gas welding, MIG uses a continuous solid wire electrode and a shielding gas of argon and carbon dioxide to protect the weld from atmospheric contamination. It’s also called Gas Metal Arc Welding because it uses gas and an electric arc to weld the filler metal.
The welder feeds the wire electrode into the weld pool using a welding gun at high temperatures during this welding method. As the wire melts in the puddle, it stimulates the joining of the metal pieces together, firming a bead-like seam at the joint.
The MIG welding method is known for its high speed, yet it creates firm and neat welds. Also, MIG welding is cost-effective, requiring no special tooling. Moreover, it’s suitable for various metal sheets, including aluminum, carbon steel, stainless steel, etc. Because of the less tooling, it is easy to learn and the go-to welding method in various manufacturing industries, including automotive, construction, aerospace, etc.
TIG Welding
Tungsten Inert Gas (TIG) is another type of arc welding. It uses a non-consumable tungsten electrode and an electric torch to effect welding. Like MIG, it also uses a shielding gas, though often pure argon or helium as the shielding gas, to prevent contamination and ensure a high-quality weld.
Sometimes, sheet metal welders may use separate filler metal in TIG welding to reinforce the seams. However, it is usually suitable for non-ferrous metals like aluminum, copper, titanium, etc., especially in the aerospace industries, among other industrial applications.
Comparing MIG vs. TIG welding, you’d notice that MIG is the faster and easier process. In fact, TIG requires some level of expertise from the welder and may be time-consuming.
Stick Welding
Like TIG and MIG, it’s an arc welding process, sometimes called – shielded metal arc welding. The process involves using electric current to melt a metal wire (a rod or stick), forming an arc between the adjoining workpieces and the electrode.
Stick welding is a manual process that does not utilize any shielding gas. Instead, as heat is produced, it disintegrates the flux covering the electrode and forms a slag that shields the weld pool.
Compared to TIG and MIG welding, it requires more expertise for control. However, it is portable and easy to carry, making it suitable for outdoor welding and inconvenient environments. That said, it is ideal for welding more rigid metals like steel and iron in construction works, shipbuilding, etc.
Plasma Arc Welding
Like TIG welding, plasma arc welding uses a tungsten electrode. However, it’s an advanced welding method that uses pressurized gas to create hot plasma for high energy concentration.
It’s also comparable to laser beam welding in that it is relatively fast, producing high-precision welding and an aesthetically pleasing weld. This makes it valuable in parts of aerospace industries, shipbuilding, construction, etc.
Laser Beam Welding
Like sheet metal laser cutting, laser beam welding is a non-contact process that uses highly focused laser beams to create a deep, narrow weld. It is relatively expensive, requiring sophisticated tooling, but highly recommendable for high-precision welding.
Laser beam welding can join small metal pieces yet maintain high dimensional accuracy. This feature makes it valuable to the medical and aerospace industry, where minimal distortion or welding defects may be detrimental.
Since it uses a laser beam, it generates high energy, making it suitable for welding tough metals like stainless steel and titanium, including thermoplastics. In addition, it generates strong weld with high aesthetic appeal, requiring little to less post-welding finish.
Gas Welding
This welding process uses heat from burning fossil fuels, gasoline, oxy-acetylene, or oxygen. The method employs heat from these fuels to melt the metal pieces and create a robust and firm weld.
Gas welding is a traditional yet effective welding method. It does not require electricity, making it cost-effective. In addition, it is excellent for joining thin sheets of aluminum, steel, copper, titanium, and other alloys.
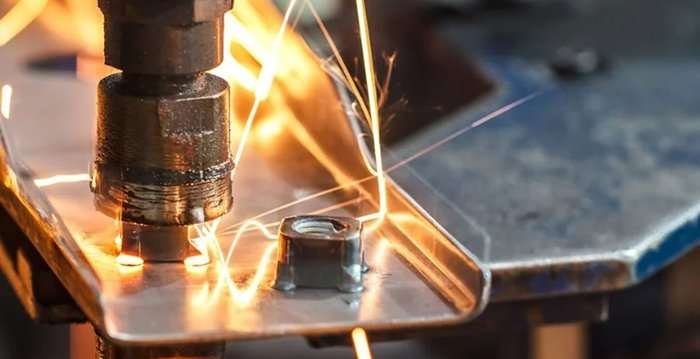
Available Metal Sheets For Sheet Metal Welding
While sheet metal welding is a highly versatile manufacturing process, it is compatible with various metals for welding. However, each metal has its benefits over others. In common, steel (including carbon steel and stainless steel) and aluminum are the most used metals for welding.
Steel possesses excellent weldability and considerable strength. Also, it’s compatible with different welding processes, including MIG, TIG, and stick welding. Aluminum’s lightweight and corrosion resistance makes it valuable for welding, especially in aerospace and automotive applications. However, it’s more difficult to weld, though compatible with various welding methods, especially TIG and MIG.
Other metals available to weld sheet metal include titanium, copper, brass, and gold. However, the use of these metals in welding is less pronounced because of cost and difficult weldability. For example, gold is the most expensive metal in sheet metal welding. On the other hand, copper and brass are preferred for decorative and electrical applications.

Surfaces to Consider When Welding Sheet Metal
When welding sheet metal, it is crucial to understand the surface orientation for achieving success and top-quality welds. Below are some surfaces you’d encounter when welding and the suitable welding methods.
Flat Surface Welding
During flat welding, the sheet metal welders weld from the upper side, pointing the torch at an angle of about 45 degrees to the surface. Flat surfaces are one of the simplest orientations you’d come across when welding since gravity aids the molten flow.
MIG and TIG welding methods are most appropriate for welding flat surfaces. Also, we recommend you move the torch in a back-and-forth motion along the seam to ensure all sides are melted for optimum welding.
Horizontal Surface Welding
From the welder’s point of view, horizontal surfaces appear flat to the welder. They exist in two forms:
(1) Groove Weld
In grove welding, the two abutting metal pieces lie at an angle. The welder presses one over the other as they weld, creating a groove-like seam.
(2) Fillet Weld
In filet weld, the welder places a metal piece over another, the end of a vertical surface pressed against a horizontal one. It usually takes a perpendicular pattern, forming an L-shaped weld.
Stick welding is the most appropriate regardless of the horizontal surface you are working with.
Vertical Surface Welding
As the name suggests, vertical welding involves welding metal pieces standing upright facing the welder. Because of gravity, molten metal tends to flow downward during welding and may even pile at the base. Therefore, it is paramount for the welder to modulate the solder and position the welding gun at 45 degrees to the adjoining metals. Again, stick welding is the most appropriate for welding vertical surfaces.
Overhead Surface Welding
It is the rarest surface orientation to weld metal sheets. It involves joining metal pieces above your head level. They are the most challenging surfaces to work with because they require precise control to prevent molten metal dripping and achieve suitable penetration. The best way to simplify this welding surface is to minimize the weld puddle and use enough filler metal.
Expert Tips For Sheet Metal Welding
Beyond understanding different methods of welding sheet metal, including the best metal for your fabrication, achieving optimal results requires precision and skills. The following are expert tips to ensure your product meets all the specifications.
Select Right Welding Technique
Each welding technique offers distinct advantages, depending on metal type, surface orientation, and manufacturing needs. That said, you must choose the best welding method for your application. In addition, consider joint complexity and metal thickness when selecting a welding method.
Choose the Appropriate Filler Metal
When welding, the filler metal you select must be compatible with the fabrication’s mechanical properties. For more efficient welding, it’s best to ensure the filler material is thinner than your metal sheet. For example, if your metal sheet is 1 mm, use a filler that’s about 0.5 or 0.6 mm.
Thick fillers often require higher heat to melt and may increase the risk of deformation, warping, and excessive heat build-up. In addition, ensure it’s thick enough to produce durable weld. You also need to consider factors like metal types, thermal expansion, corrosion resistance, and mechanical features of the filler to reduce the chances of welding defects. For example, an aluminum sheet will require a thicker filler than steel.
Use a Small Wire Diameter
It’s best to stick to smaller wire diameters when welding using solid wire electrodes, as in MIG welding, especially if you are still gaining experience. This affords you better heat control and reduces the chances of welding defects or burning through your metal sheets.
Apply Skip Welding Technique
This technique involves making a series of short intermittent welds (or stitches) at strategic points on metal sheets. Then after allowing it to cool for a few minutes, the welder can weld the skipped areas. Skip welding technique is beneficial in lengthy seams, helping to prevent excessive heat build-up, distortion, and warping.
Use Argon-base Shielding Gas
It’s best to use shielding gas with a high percentage of argon when welding. Unlike oxygen, argon is an inert gas; therefore, it doesn’t interfere with welding or cause rusting. A typical example is the mixture of argon (75 percent) and CO2 (25 percent). In fact, pure argon gas can also serve as a shielding gas with TIG and MIG welding.
Apply Tack Welding Method
Like skip welding, tack welding involves creating small, temporary welds – tacks, to hold workpieces together before the firm and final weld. It is another excellent technique that helps prevent burn-through and excessive heat build-up. Just maintain a small gap of about 1 mm between adjoining metal pieces before creating tack welds. Also, it aids joint alignment and welding precision.
Avoid Over-heat
Indeed, heat is the most integral factor for welding; however, we cannot overemphasize the harmful effects of excessive heat when welding. It can melt the workpieces or create welding defects, like warping and distortion. Therefore, it is critical to control the heat output when welding.
For example, gas welding generates high heat, so it’s best for stronger metals like steel. On the other hand, stick welding will better suit thinner materials like aluminum. In like manner, with TIG and MIG welding, pulsing the weld currents helps control the heat output.
Choose XinCheng to Meet Your Sheet Metal Welding Needs
Understanding the different welding methods and their working principles is not enough. Working with a reliable partner is your best bet at achieving a fabrication that meets all your specifications, especially for those with tight tolerances.
At XinCheng, we offer premium sheet metal fabrication services. Regardless of your strict manufacturing needs, our engineers will provide effective machining solutions with cost-effective and high quality. Upload your CAD file and get a free quote today!
Read More: Choose CNC Machining Services in China
Conclusion
Sheet metal welding is a vital and versatile process crucial to various aspects of manufacturing. We often need to join different metal pieces to create more sophisticated structures. That said, like all manufacturing processes, it may seem complex, but it’s pretty straightforward, especially after gaining expertise and adhering to its principles.
FAQs
What is the best sheet welding method?
The best welding method for sheet metal depends on metal type, thickness, joint configurations, surface orientation, and fabrication requirements. However, TIG is the most appropriate when welding thin metals because of its precise hag control and versatility, offering you a satisfactory weld.
Should you use direct current or alternating current for aluminum MIG welding?
Either current is suitable for aluminum MIG welding. However, using direct current for MIG welding is faster because it does not require specialized tooling.
How can you prevent warping in sheet metal welding?
Ensuring control of heat output is integral for minimizing warping. Effective welding techniques for this include tack and skip welding. Also, consider clamping the workpiece for quick heat dissipation.